Rapid Prototyping
Overview
At Holmes-Gustafson & Associates, LLC we understand and can recommend a proper use of rapid prototyping to produce full scale prototypes of new designs to verify the fit and function of your product.
Below are just a few of the benefits and options for rapid prototyping:
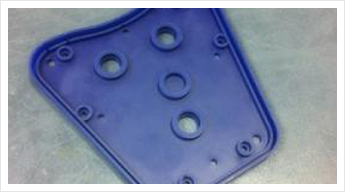
Stereolithography is an additive manufacturing process which utilizes a vat of liquid resin and a laser to build parts a layer at a time to create a 3D part. The laser traces each part on the surface of the resin to solidify it. That piece then drops down into the resin to create another layer (.002″ to .006″). A blade then sweeps across the part to insure even distribution of the resin. Again the laser traces the part to solidify the resin and adhere it to the previous layer. The process is repeated until the build is complete; the parts are then cleaned and cured in a uv-oven (PCA). SLA parts are very accurate and have the best surface finish of the common prototyping technologies.
Selective Laser Sintering (SLS) is an additive manufacturing process that creates 3D components from powdered material. A laser is used to heat and fuse the powder one layer at a time, creating a solid structure.
Laser sintering produces functional production components, eliminating the need for tooling and the investments of time and capital that go along with it. This leads to economic savings and quick turnaround as parts can be ordered with short lead times and with no penalty for design changes.
The final components are ideal for use in harsh environments and demanding applications.
Contact Holmes-Gustafson & Associates at (815) 985-5116 to learn more about the advantages of rapid prototyping.